Modellsegelboot
Ein Beitrag von Jörg Frenzel (Freie Waldorfschule Kaltenkirchen)
Modelle haben mich schon immer fasziniert, besonders Segelschiffsmodelle. Schon als Kind sammelte ich Holzstücke am Strand und bastelte daraus eine kleine Flotte, die ich dann schwimmen ließ, bis die Sonne unterging. Interessant fand ich später die Beziehung von Ästhetik und Funktionalität. Was gut aussieht, funktioniert auch gut und umgekehrt. Es macht einfach Spaß, sich in eine Form zu vertiefen, sich in sie hinein zu versetzen und ihr Verhalten im Wasser zu studieren. Fertige Bausätze reizten mich weniger, da sie einem nicht den Raum zum Experimentieren und zum Selbstentwickeln lassen. Diese Freude am Entwickeln und Bauen wollte ich gerne an die Schüler weitergeben und habe für die Projektwoche 2019 an unserer Schule die Anfertigung dieses Modell angeboten, das ich mir eigens dafür ausgedacht und einmal komplett vorgebaut habe.
Ich hatte dabei an die Altersgruppe der 6. bis 9. Klasse gedacht. Die Erfahrung während der wenigen verfügbaren Tage (ein Feiertag dazwischen) zeigte allerdings, dass die Mittelstufe doch damit überfordert war. Drei Jungen aus der 9. Klasse machten sich gemeinsam an den Bau eines Modells, konnten es aber in der knappen Zeit nicht fertigstellen. Ich habe daraufhin einen Modellbaukurs im Rahmen des handwerklich-künstlerischen Unterrichts angeboten. Die Jungen hatten keinerlei Vorkenntnisse und waren über den Umfang und auch die auftretenden Schwierigkeiten überrascht. Hier musste ich öfters mit Hand anlegen und motivieren. Modellbau stellt hohe Anforderungen an genaues Arbeiten, Findigkeit in der Lösung von Problemen, den richtigen Umgang mit den Materialien und natürlich auch an Geduld und Durchhaltewillen. Hier sollte der anleitende Lehrer / Projektleiter mit seiner Erfahrung und Begeisterung für die Sache stützend wirken. Die geringe Frusttoleranz und Neigung, sich immer wieder Ablenkungen hinzugeben, erscheint mir typisch für dieses Alter und vielleicht besonders auch für die Zeit, in der wir leben. Aber ich bin mir sicher, dass es – wenn das Boot dann schließlich auf dem Wasser seine Bahn zieht – die jungen Modellbauer mit Freude und Stolz erfüllen wird!
Hier ist ein YouTube-Video eingebunden. Damit dieses angezeigt werden darf, wird Ihre Zustimmung benötigt. Alle datenschutzrelevanten Details dazu sind in der Datenschutzerklärung vermerkt.
.
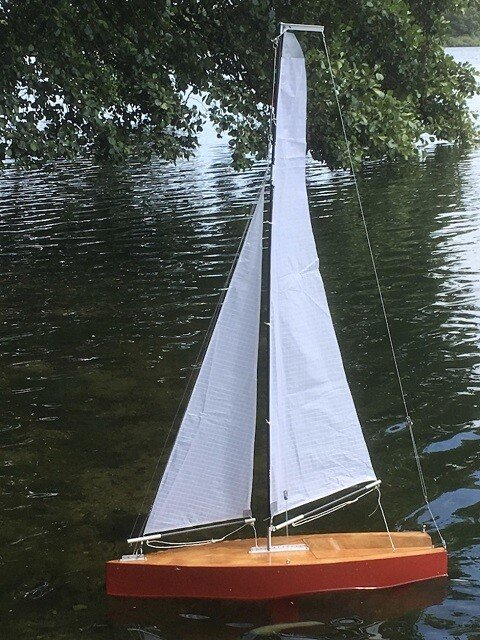
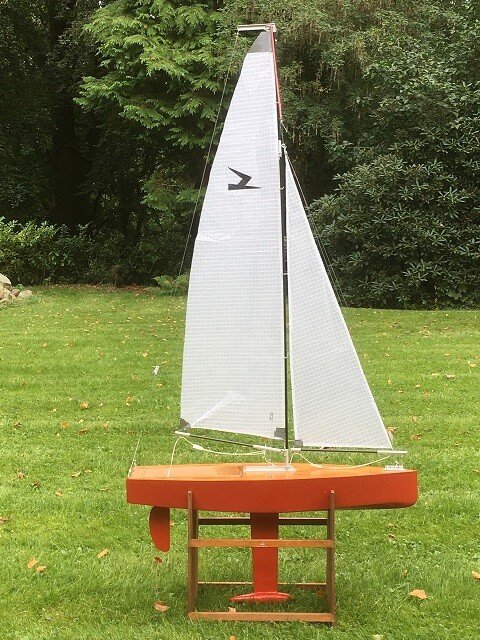
Bauanleitung
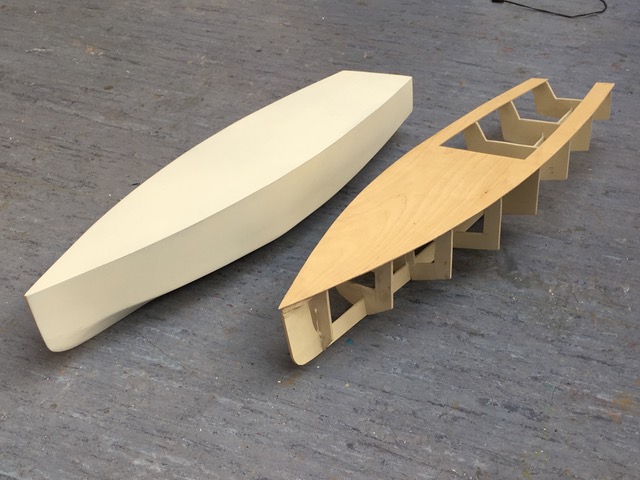
- Ausschneiden der Teile kann u.U. nur vom Lehrer gemacht werden kann
- Stichsäge gerade bei flattrigem Sperrholz nicht ungefährlich
- beim Ausschneiden kommt es vor allem auf Genauigkeit an, da sonst die Teile nicht passen
Bild: Prototyp aus Karton (links), Rumpf im Rohbau (rechts), Deckoberseite mit Aussparung (Plicht), Spanten (Rippen) und Kiel (Rückgrat eines Schiffes)
Die Bauschritte
Ausschneiden der Bauteile und Glätten
- Umrisse des Decks mit Schablone und spitzem Bleistift auf das dünne Sperrholz ( 2 mm)
- übertragen und mit der Stichsäge exakt ausschneiden. (möglichst materialsparend!)
- Genauso verfahren mit den Spanten (1 – 8) auf Pappelsperrholz (4 mm)
- und Kiel auf dickem Pappelsperrholz (evtl. aus 2 Ausschnitten zusammenkleben)
- Ränder mit Schleifklotz etwas glätten
I Montage des Rumpfskeletts
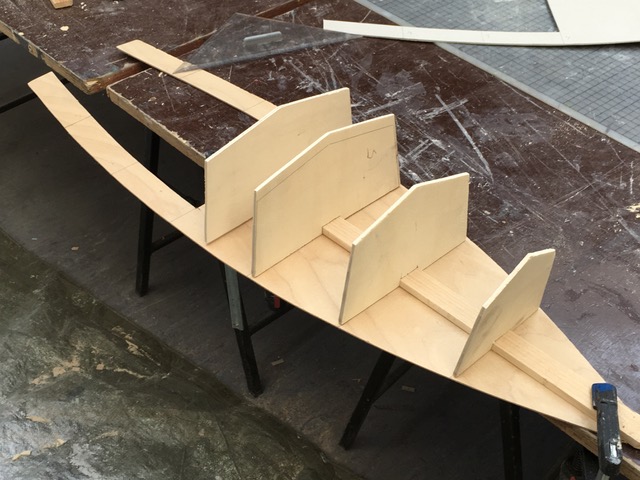
1. Abstände der Spanten mit Bleistift auf Decksunterseite übertragen (10 cm gemäß der Zeichnung)
2. Decksverstärkung (Leiste 2,3 cm) mit Handsäge passend zuschneiden (vorne spitz, 2 mm Decksüberstand) und auf Unterseite des Decks genau mittig (vorher Mittellinie mit Bleistift markieren!) aufleimen
3. Spanten 5 – 8 probeweise auf die Leiste in den richtigen Abständen aufstecken. Achten auf Passgenauigkeit (evtl etwas nachschleifen), richtige Fluchtung der Seiten und Ecken, genügend Decksüberstand ca 3 mm, wird später abgeschliffen) dann Spanten 4 – 8 an den Schnittkanten mit PONAL vorleimen und trocknen lassen, nochmal Leim auftragen und absolut gerade und rechtwinklig (Kontrolle mit Geodreieck oder zugeschnittenem Kartonstück!!!) auf das Deck aufleimen.
4. Leiste (2,3 cm) für Spanten 1 – 4 passend abschneiden und darauf die Spanten stecken (Passgenauigkeit und Fluchtung von Seiten und Ecken prüfen!) Auflage der Leiste an Spante 4 mittig aufkleben. Schnittkanten der Spanten vorleimen und nach Trocknen Leiste in die Nut einkleben. (wieder
auf die rechten Winkel achten! Spanten auf gerader Fläche ausrichten!) dann die durch die Leiste verbundenen Spanten 1- 4 auf die Unterseite des Decks aufkleben.
Nun sollten alle 8 Spanten genau parallel rechtwinklig zum Deck fest angeklebt sein. Die beiden Leisten sollten genau mittig parallel zum Deck in einer Flucht verlaufen. Kein Spant darf in Höhe und Breite vor- oder zurückspringen!
5. Umlaufende Eckleisten (20 mm x 4 mm) mit Schleifpapier glätten und in die Aussparungen der Spantenecken (Vorleimen nicht vergessen!) einkleben. Die Leiste endet mit Spant 8. Dabei beachten, dass die Spanten parallel und rechtwinklig bleiben. Vorne und hinten werden die Leisten bis zum Trocknen des Leims mit Schraubzwingen (klein) zusammengehalten.
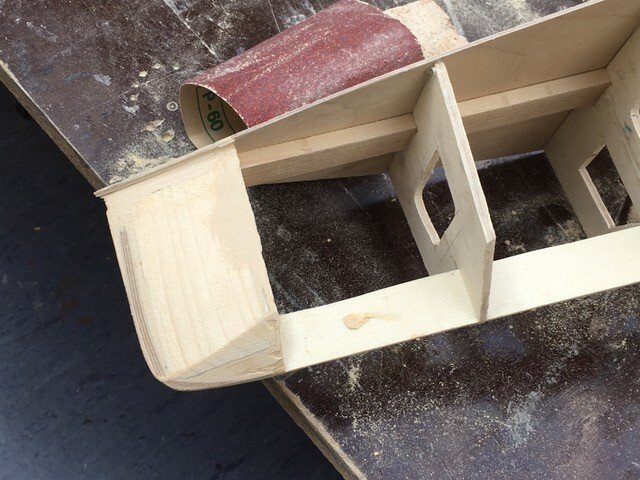
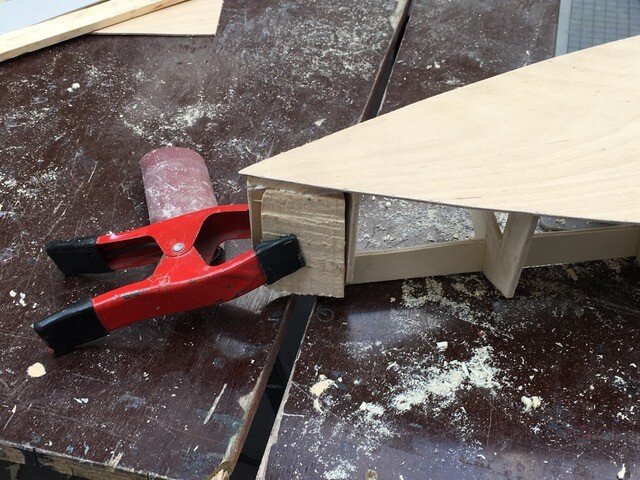
6. Aus einem auf Länge geschnittenen Stück Dachlatte 2 Keile sägen, die in beide Seiten des Bugs geklebt und nach dem Trocknen durch Raspeln und Schleifen angepasst werden. Der Bugbereich muss komplett mit Holz ausgefüllt sein, um genügend Klebefläche für die Seiten zu bilden. Lücken werden mit Spachtelmasse verfüllt.
7. Leiste (2,3 cm) zwischen Spant 1 und 2 passend einkleben. (notwendig für die Führung des Ruders). Dazu den Kiel der Dicke der Leiste entsprechend ausklinken. (mit dicht gesetzten Sägeschnitten, die dann mit einem Holzbeitel entfernt werden). 2 Leistenstücke in die hinteren Ecken kleben (als Auflage der späteren Rumpfseiten)
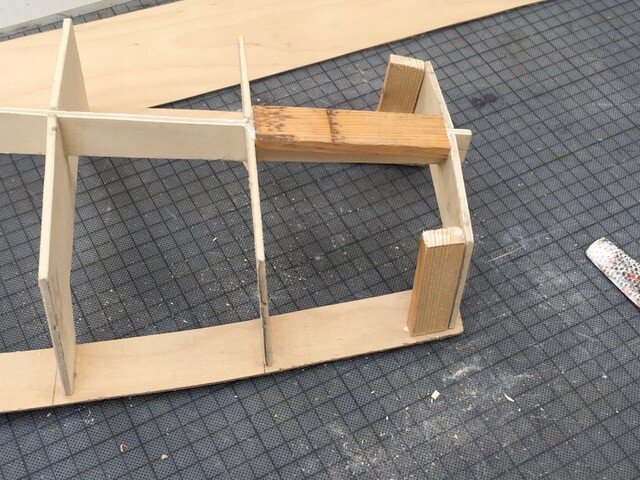

8. Kiel zwischen Spant 4 und 5 mit Handsäge entfernen und durch 2 senkrechte Brettchen ersetzen (8 mm Sperrholz). Sie müssen genau zwischen die Spanten 4 und 5 passen. Beide werden dann genau so eingepasst, dass der Ballast-Kiel knapp hineinpasst. (den machen wir aus Plexyglas, weil ohne
Auftrieb und wasserfest) ein Brettchen wird genau senkrecht eingeklebt. (Das zweite erst später. So entsteht ein unten offener Kasten, in den der Ballastkiel später eingeschoben werden kann)
9. Leistenstücke (2,3 cm) links und rechts zwischen Spant 4 und 3 an Unterseite des Decks kleben. (damit man später von oben Ringbolzen für die Wanten. einschrauben kann)
10. Alle Kanten nun gründlich mit Schleifklotz angleichen (anschrägen) und glätten. Die später aufgeleimte Außenhaut muss überall gleichmäßig
anliegen. (mit geradem Brettchen oder Leiste kontrollieren!)
Dein Boot sollte jetzt so aussehen!
II Aufbringen der Außenhaut
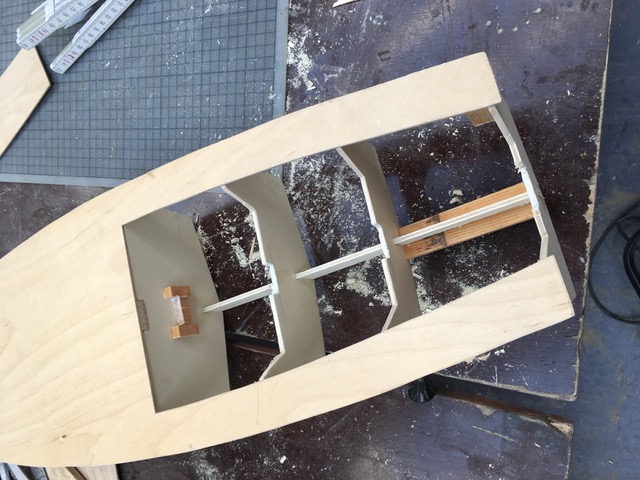
Knifflig! Das recht schwer biegbare dünne Sperrholz muss nun an das Rumpfskelett angepasst und angeklebt werden. Das gelingt nur mit guten Nerven, Genauigkeit und einem gewissen Kraftaufwand, da das Holz nur unter starker Spannung gebogen werden kann. Dafür muss man genau beachten, dass keine Lücken entstehen, die den Zusammenhalt gefährden! Immer vor dem endgültigen Verleimen ausprobieren, ob es auch passt!!!
1. Die beiden Rumpfseiten werden mit der Schablone auf das dünne Sperrholz (2 mm) übertragen und mit der Stichsäge ausgeschnitten. (die Aussparung für den Ballast-Kiel-Kasten nicht vergessen!)
2. Spanten gut gerade schleifen Umlaufleiste, Kiel, Kielkasten, Bugbereich und Ruderführung der Spantenausrichtung anschrägen, sodass eine gleichmäßige Auflage gewährleistet ist! und vorleimen.
Überprüfen, ob das Seitenstück sich überall gleichmäßig an das Rumpfskelett anschmiegt. Vor allem zwischen Deck und Seitenkante dürfen keine Lücken entstehen. Das würde die Stabilität und Dichtigkeit des Rumpfes gefährden.
3. Wenn alles gut passt, Rumpfseiten mit 2 Schraubzwingen und einer Andruckleiste, die über die ganze Seite läuft und das Holz überall andrückt, an die Spanten und das Deck anleimen. Mehrere Zwingen auch so setzen, dass die Bordwand auf das Deck gepresst wird und hier keine Lücken entstehen.
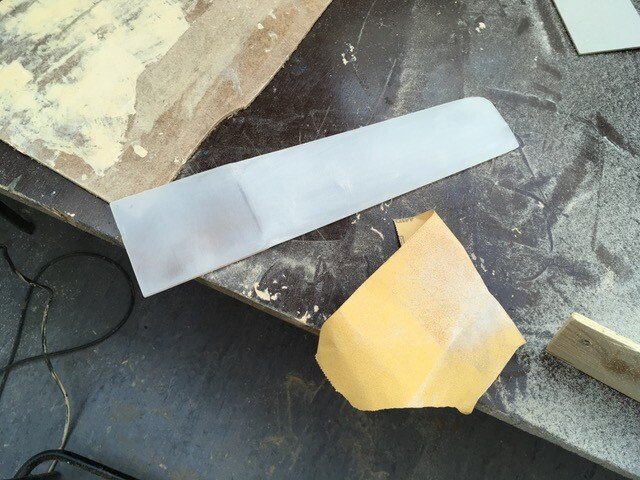
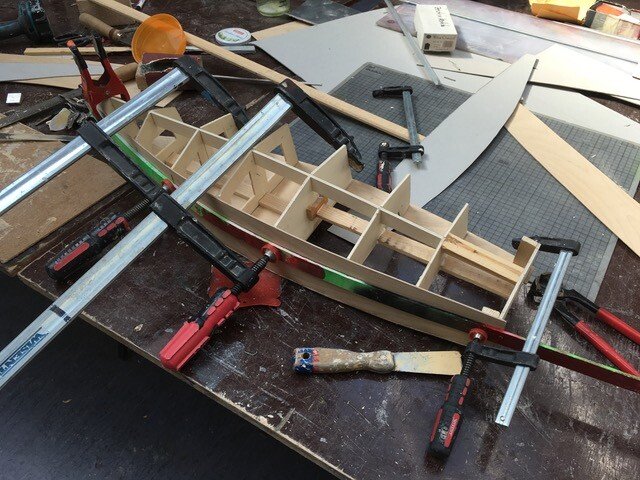
4. Weil das Ganze unter Spannung steht, sollte der Leim lange durchhärten. Am besten 1 Tag. In der Zwischenzeit können wir den Ballast-Kiel und das Ruderblatt aus Plexyglas auschneiden (Schablone) und im Profil tropfenförmig schleifen, soweit sie aus dem Rumpf herausagt. Das geht gut mit einem Winkelschleifer und aufgesetztem Schleifteller. Die ausgeschnittene Flosse wird mit einer Schraubzwinge am Tisch befestigt. (natürlich kann auch anderes Material als Plexyglas verwendet werden. Ich hatte es gerade auf Lager. Wichtig ist Stabilität. Ich denke, es wird auch mit schichtveleimten Holz von 0,8 – 1 cm Stärke gehen.)
5. Nach Durchhärten des Leims Zwingen entfernen und den Innenraum mit Epoxid-Harz ausstreichen, besonders die Ecken zwischen Bordwand und Deck. Auch die Innenseite des Kielkastens, damit dieser wasserdicht wird. (es wird auch ohne EH funktionieren, falls dieser nicht vorhanden ist. Hauptsache ist, dass der in den Bootskörper am Ende wirklich kein Wasser eindringen kann. Lücken und Spalten in der Außenhaut lassen sich kaum ganz vermeiden, lassen sich aber später gut mit 2Komponenten-Spachtelmasse (Feinspachtel aus dem Baumarkt) schließen, schleifen und lackieren.
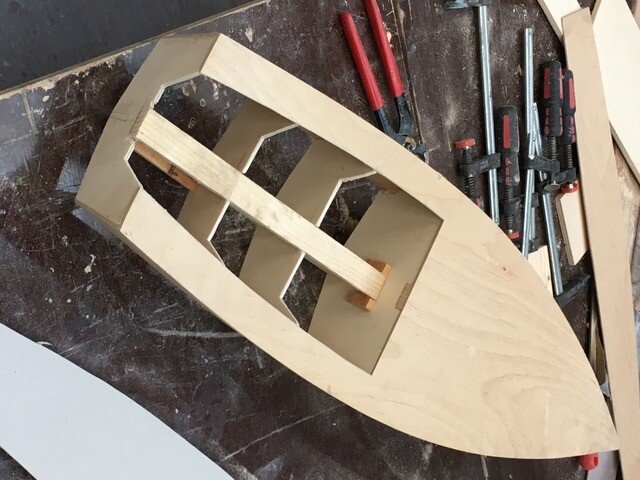
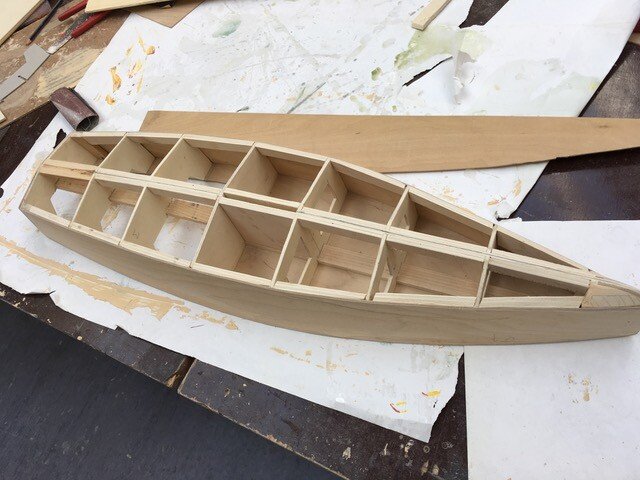
6. Spiegel aus dünnem Sperrholz wie Spant 1 ausschneiden und auf die Rückseite des Rumpfes kleben und nach dem Trocknen die Überstände abschleifen.
7. Ankleben der Bodenstücke beide Bodenstücke aus dünnem Sperrholz ausschneiden und mit Schleifpapier glätten. Im Bereich des Kielkastens eine Aussparung von jeweils 2 mm einbringen. Mit Bleistift Mittellinie auf dem Kiel anzeichnen. Beide Hälften auflegen und prüfen, ob sie sich entlang der Mittellinie lückenlos aneinander legen lassen und keine Lücken entstehen. Stark saugende Stirnflächen zu verklebender Holzteile sollte man unbedingt einmal vorleimen und anschließend 10 Min. trocknen lassen. 1. Hälfte mit Epoxid-Harz (oder Ponal-Blau), Schraubzwingen und Andruckleiste aufkleben und 1 Tag trocknen lassen. Genauso verfahren mit der 2. Hälfte.
Das Anleimen der Außenhaut – also Seiten und Bodenplatten – gehört wegen der Spannung zu den kniffligsten Aufgaben des ganzen Bauprozesses! Hier sollte man Geduld und kühlen Kopf bewahren. Man braucht eine genügende Anzahl von guten Schraubzwingen und eine biegsame Latte, um den Druck gleichmäßig auf alle Spanten zu verteilen. Die Zwingen müssen so groß sein, dass sie Bootskörper und Tischunterseite gut verbinden können. Auf jeden Fall einen Tag vorm Lösen verstreichen lassen!
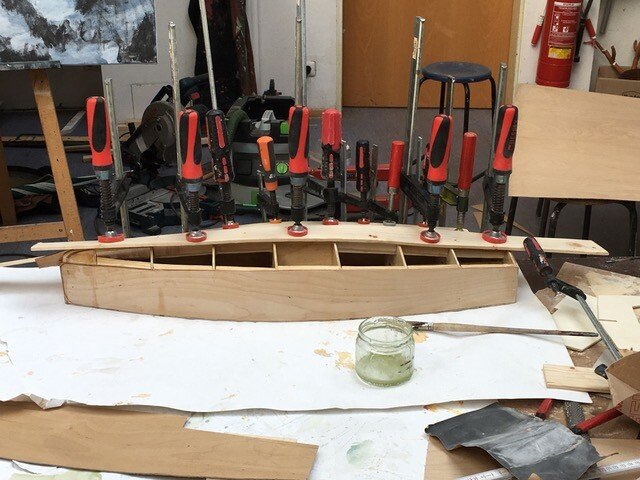
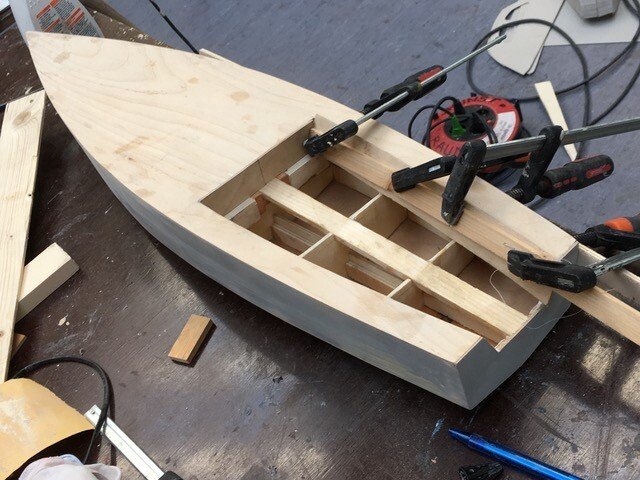
8. Schleifen und Verspachteln des Rumpfes
Nach dem Lösen der Zwingen werden überstehende Teile (wie z.B. das Deck oder über den Spiegel ragende Seiten) werden nun mit Schleifklotz (oder Hobel bei langen stark übertretenden Partien) auf ein Niveau gebracht. Eine schöne Arbeit, weil nun der Bootskörper schon seine geschlossene, endgültige Form erahnen lässt. Spalten werden mit Spachtelmasse verfüllt und nach dem Durchtrocknen wiederum sauber verschliffen und auf Form gebracht.
III Weitere Bauschritte
1. Einleimen der Plicht
Auf der Innenseite werden nun passend zugeschnittene Streifen von 2mm Sperrholz (dasselbe wie für die Außenhaut) in der abgebildeten Weise aufgeleimt und anschließend der Überstand abgesägt und beigeschliffen.
2. Anbringung der Ruderführung und des Ruders An der auf der Zeichnung angegeben Stelle wird mit dem Akkuschrauber/bohrer ein genau senkrechtes Loch durch die Mittelleiste und den Boden gebohrt. Hier braucht man Augenmaß und eine ruhige Hand, um das Loch genau senkrecht zu führen. (Möglich – wenn vorhanden – ist natürlich auch eine Standbohrmaschine, geht aber auch freihändig). In das Loch wird nun ein passendes Stück des Alu-Rohres ø 0,8 cm mit Spachtel eingeklebt. (gut um den Fuß des Rohres verstreichen, damit hier später keine undichte Stelle entsteht) In dieses Rohr sollte die im Ruderblatt eingeklebte Gewindestange genau passen, sich also leichtgängig bewegen lassen ohne zu wackeln.
Das Ruder wird entsprechend der Zeichnung aus Plexilglas oder Schichtholz ausgeschnitten und wie die Flosse tropfenförmig geschliffen, um den Wasserwiderstand zu minimieren. (auch vom optischen Standpunkt wichtig!)
In das Blatt mit der Stichsäge einen Spalt schneiden, sodass die Gewindestange gerade hineinpasst. Stange mit Zwinge am Tisch fixieren (oder Schraubstock) und so mit Metallsäge auf Länge schneiden, dass sie gerade soweit aus dem Führungsrohr ragt, dass noch eine Mutter + Unterlegscheibe aufgesetzt werden kann. Sie darf natürlich nicht zu lang sein, da sich sonst die spätere Abdeckung nicht schließen lässt. Nun das Gewindestangenstück in den Spalt im Ruderblatt mit Spachtelmasse einleben und verschleifen.

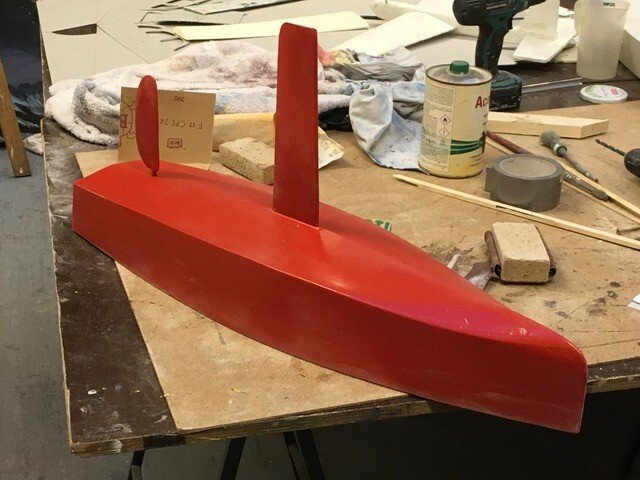
3. Einkleben der Flosse
Mit Spachtelmasse wird nun die Flosse in den dafür vorgesehenen Kasten geklebt und die Lücken am Übergang zum Rumpf sorgfältig verstrichen. Die Flosse muss natürlich absolut senkrecht stehen (was beim genauen Arbeiten des Kastens natürlich von sich aus der Fall ist) und etwas nach hinten geneigt sein. Hier kann man sich auf sein „optisches Gefühl“ verlassen.
4. Schleifen des Rumpfes und Lackieren
Nun kann alles sauber verschliffen werden. Zuerst grobes (80er) dann feineres Schleifpapier (120er sollte reichen). Im Anschluss empfiehlt sich eine gute Schicht Sprühspachtel. Er schließt die Holzporen und bietet eine gute Grundlage für die anschließende Lackierung. Ich habe für die abgebildete Lackierung roten Hochglanzlack verwendet, denn ich mit dem Pinsel aufgetragen habe. Das Deck habe ich naturbelassen mit Klarlack lackiert. Die Kombination der Holzmaserung mit dem roten Rumpf sind ziemlich gut aus! Mit Holzbeize (teak) lässt sich die Maserung vor der Lackierung natürlich noch gut steigern. Das Holz bekommt einen warmen vollen Ton und die Maserung tritt stärker hervor. Dann mit feinem Papier schleifen und lackieren.
5. Anfertigung der Plichtabdeckung aus 4 mm-Sperrholz entsprechend der Zeichnung.
Damit sich die Abdeckung dicht schließen lässt, eine ensprechende Leiste an der Außenseite von Spant 4 ankleben, sodass der Deckel genau in den entstehenden Spalt passt. Hinten klebt man in die Mittelleiste (hinter der Ruderführung) ein Stück Gewindestange ein, die durch ein Loch des Deckels führt. Dieser lässt sich dann mit einer passenden Flügelschraube gut verschließen. (Unterlegscheibe auf den Deckel kleben!)

6. Beschläge und Mastherstellung
An den bezeichneten Stellen werden kleine Augbolzen eingeschraubt. (vorher das Gewinde in etwas Leim tauchen). Mast und Fock-/ Großbaum werden entsprechend den Maßen aus der Zeichnung aus 6 mm Carbonrohr (gibt es im Drachenladen oder im Internet) zugeschnitten. Die Einden werden mit Alurohr verstärkt, in das das C-Rohr genau passend eingeschoben werden kann. Für eine saubere, schnell trocknende und sehr feste Verbindung empfielt sich Sekundenkleber. (Achtung! Er verklebt auch Haut in Sekundenschnelle!) In die entsprechend vorgeborten Alu-Verstärkungen lassen sich auch gut kleine Augbolzen einkleben (vorher auf entsprechende Länge sägen). Der Mast wird mit einem Stück Alurohr aus 2 Teilen zusammengesetzt, da C-Rohr üblicherweise nur bis 100 cm geliefert wird. Die Verbindung dient gleichzeitig der Aufnahme der Augbolzen für Wanten
und Vorstag.
Für sicheren Stand und Vermeidung von Beschädigungen der zerbrechlichen Flosse und des Ruderblattes empfiehlt sich der Bau eines Ständers gemäß der Zeichnung!
Die Mastführung und Bugbeschlag werden aus einem Stück Alu-T-profil angefertigt. Dazu ein ca. 10 cm langes Stück absägen und im Abstand von 1 cm Löcher ø 1 mm bohren. Für die Befestigung auf dem Deck vorn und hinten je ein Loch ø 1mm bohren. Nun wie in der Abbildung auf das Deck mit kleinen Rundkopfschrauben anschrauben. Der Mastfuß wird eingeschlitzt und passt so genau auf die Mastführung. So lässt sich später der Segelschwerpunkt nach vorn oder hinten verschieben, sodass das Modell optimal auf den Wind und das Ruder reagiert (also weder luv- noch leegierig ist) Für den Bugbeschlag (Befestigung des Vorstags und Fockliek) ein entsprechend kürzeres Stück) Das stehende Gut (Vor-, Achterstag, Wanten) lässt sich gut aus Dralonschnur anfertigen (klare 1 mm starke Schnur), Sehr reißfest, „ribbelt“ nicht auf an den Enden. Lässt sich gut mit Klemmhülsen ohne Knoten anbringen. Haltbar und opisch vorteilhaft gegenüber „Knoten“. Geht aber natürlich auch mit festem Kunstfaser-Seil aus dem Baumarkt. (ø 1mm) Für das laufende Gut (Steuerung der Segel) eignet sich dünne geflochtene Dralon-Schnur ø 1 mm.7. Anfertigung der Segel Für die Segel eignet sich am besten Drachenstoff. Gibt es in Drachenläden oder im Internet. Sehr leicht, reckt sich nicht, windundurchlässig, feuchtigkeitsresistent.
Fock und Großsegel entsprechend der Zeichnung ausschneiden. (kann man mit einem Lötkolben machen, was den Vorteil hat, dass die Kanten nicht mehr ausfasern können) Dazu etwa 1 cm Saum lassen. Der wird mit einem Doppelklebeband (klar, gibt es in Drachenläden / Internet) zusammengeklebt. (klebt erstaunlich fest und sauber!)
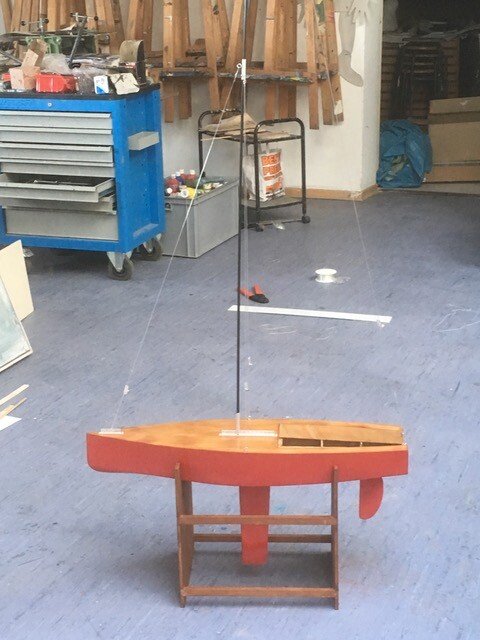
Vorliek von Fock und Großsegel nimmt hier ein 1 mm starkes Seil als Verstärkung auf, das gleichzeitig oben und unten der Befestigung dient. Die Ecken der Segel werden durch aufgeklebte Plastikdreiecke verstärkt. Bohrungen macht man mit einer erhitzten Nadel.
Stehendes Gut (Wanten und Stagen zur Fixierung des Mastes)
Führung der Schoten (laufendes Gut zur Steuerung der Segel) siehe Zeichnung!
8. Gießen und Anbringung der Bleibombe
Das hatte ich auch vorher noch nie gemacht, stellte also auch für mich eine echte Herausforderung dar. In diesem Fall klappte es aber BESSER als erwartet! Im Idealfall wiegt der Rumpf einer Segelyacht gar nichts und der Ballast, also der Gewichtsanteil am untersten Teil des Schiffes ALLES! Das kann man sehr gut an den modernen Carbon-Rennern ablesen, wie sie z.B. im Volvo-Ocean-Race in den letzten Jahren zum Einsatz kommen. Der Ballast hängt in Form eines tropfenförmigen Bleigewichts am unteren Ende der Flosse und wirkt dem selbst bei einem Modell erstaunlichen Segeldruck entgegen und verhindert so, dass sich das Boot bei der ersten Brise platt aufs Wasser legt oder sogar komplett durchkentert. Steh-auf-Männchen-Prinzip!
Es soll diese Gewichte auch fertig im Internet geben, sind aber teuer! Viel reizvoller und vor allem preiswerter ist die Eigenvariante. Blei gibt es z.B. im Schrotthandel. Ich habe einfach im Internet unter „Altblei“ geschaut und fand auch gleich einen Handel um die Ecke. „Komm einfach mal längs...!“ und eine halbe Stunde später hatte ich mehr als ich brauchen konnte. (für fünfzehn Euro) Für unser Modell habe ich ca. 900 g an Blei verarbeitet. Zum nötigen Gewicht gelangte ich durch Versuche, bei dem ich einfach die optimale Menge mit Klebeband an der Flosse anbrachte und im See Schwimmversuche machte. Ich war erstaunt darüber, welches Gewicht dieses kleine Boot scheinbar mühelos verkraften konnte, ohne zu tief einzutauchen. Das aufrichtende Element von einem knappen Kilo ist ganz enorm!
Aus einem Styroporrest habe ich eine spindelförmige Form geschliffen (Raspel und dann Schleifpapier – ging supereinfach) und dann durch Eintauchen in ein randvoll mit Wasser gefülltes Gefäß das Volumen ermittelt, indem ich das überlaufende Wasser auffing und abmaß. Mit der Bleidichte con 11,3 kg / 1000 cm³ ließ sich so das zu erwartende Endgewicht ermitteln.
Bau des Gießkastens und Abguss
Aus OSB-Resten einen Kasten bauen, der sich leicht wieder demontieren lassen kann. Die Styropor-Form wird mit 2 langen Holzschrauben „schwebend“ im Kasten fixiert. Form und Kastenkann man etwas mit Speiseöl einfetten. Jetzt fülle ich mit flüssig suppenartig angemischtem Gips (muss gut gießbar sein!) den Kasten bis zur Hälfte der Form auf und lasse es aushärten. Auf die ausgehärtete Schicht (geht meist schon nach 30
Minuten) etwas Öl zur besseren Trennung pinseln und wieder mit Gips die 2. Schicht aufffüllen. Aushärten lassen und die beiden Hälften trennen. (Siehe Foto) Mit Raspel in beide Hälften Vertiefung einarbeiten, die ein Brettstück mit der Stärke der Flosse aufnehmen kann.
So entsteht beim späteren Gießen mit Blei eine passgenaue Nut, in die ich die Flosse einkleben kann. Fertig ist die 2teilige Bleigießform!
Meine größte Sorge war natürlich die Reaktion der noch wasserhaltigen Gipsform auf das Befüllen mit flüssigem Blei! Hiervor wurde auch im Internet eindringlich gewarnt. Im harmlosesten Fall würde das blitzartig verdampfende Wasser das Blei mit Blasen durchsetzen und eine höchst amorphe Form entstehen lassen – eher einem Hackbraten ähnlich. Im schlimmsten Fall würde einem die ganze Geschichte um die Ohren fliegen. Um das zu vermeiden, habe ich die Formen im Backofen bei 200° so lang erhitzt, bis beim Öffnen der Klappe kein allzu starker Dampf mehr entwich. (beim 1. Mal habe ich vor lauter Dampf die Küche nicht mehr gesehen!)

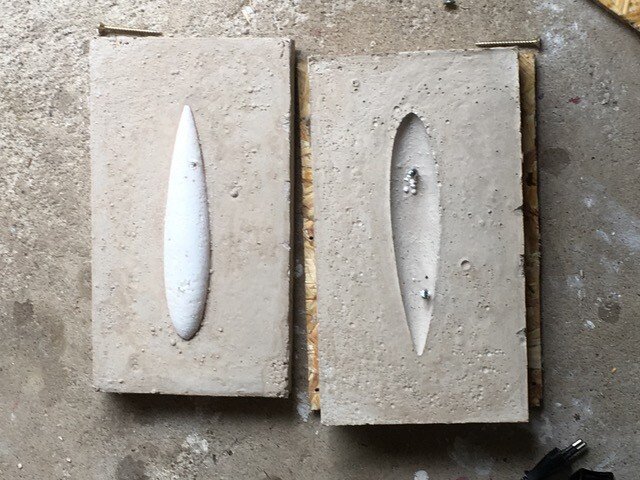
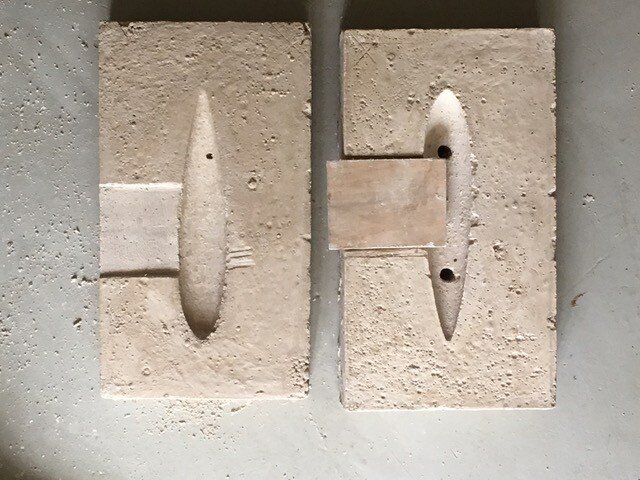
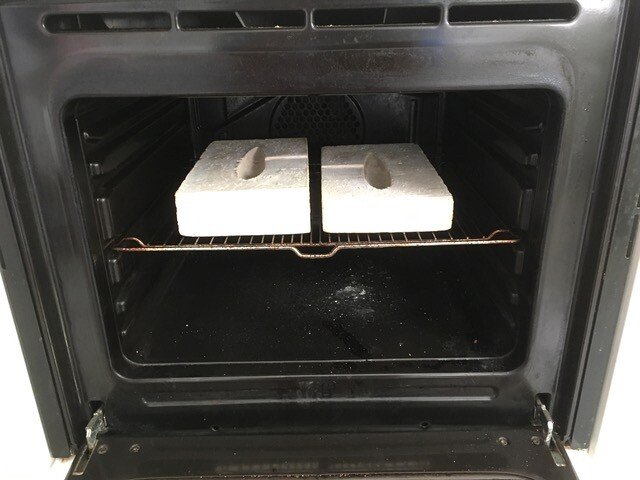
Die durch die Schrauben schon bestehenden Löcher werden auf 10 mm aufgebohrt und auf der Oberseite mit der Raspel ein „Gießtrichter“ eingearbeitet. Die so präparierte Form mit Schraubzwingen fest miteinander verbinden. Das Blei (etwa gut 1 Kilo) in einem Topf erhitzen. Ich habe dazu einen „Vorwärmer“ benutzt, die sich an eine handesübliche Propangasflasche anschließen lässt. Blei wird schon bei wenigen Hundert Grad dünnflüssig und lässt sich gut in den Trichter einfüllen, bis es im anderen Loch wieder hochsteigt. Nach kurzem Erkalten kann ich die Formen trennen und das Ergebnis sieht dann wie im folgenden Foto aus:
Mit der Flex oder Eisensäge werden die Gießkanäle abgetrennt und das Ganze mit Winkelschleifer (Schrubbscheibe) oder Eisenfeile in Form gebracht. Nun kann die fertige Bleibombe mit Spachtelmasse an der Flosse angeklebt werden. Spalten gut verstreichen. Die Flosse sollte gut in die Nut passen. Ggf. nacharbeiten. Hält prima und sieht gut aus!
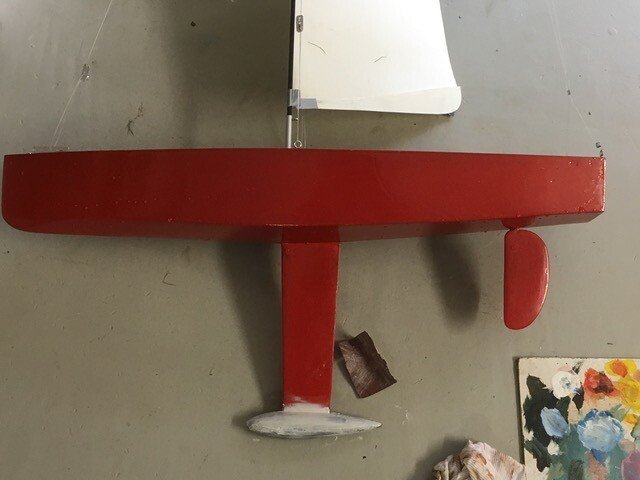
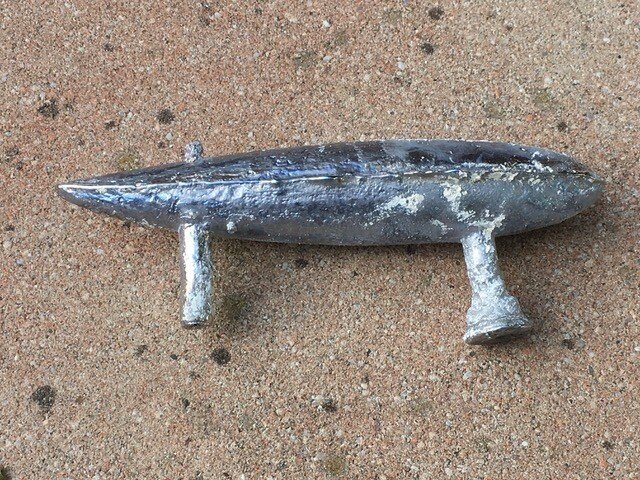
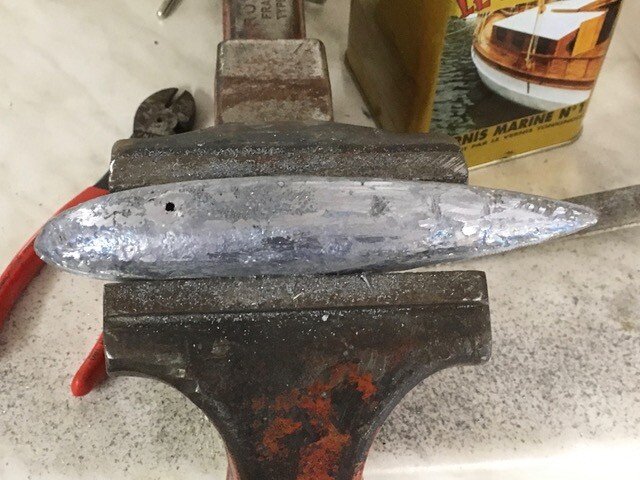
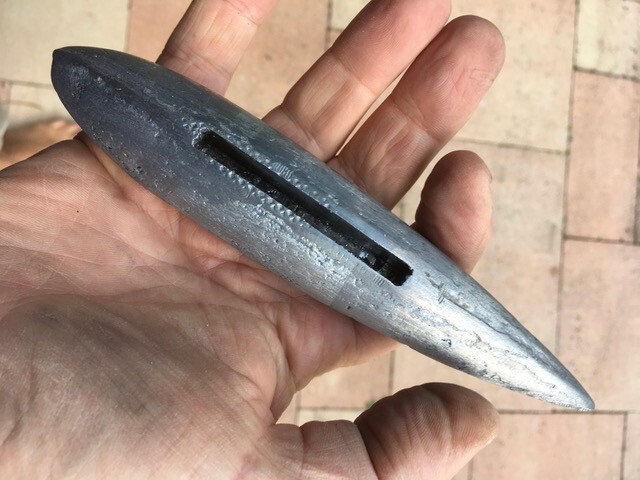
So liegt das fertige Modell mit Bleigewicht, Fernsteuerung und Batterien im Wasser. Das wird durch das relativ geringe Gewicht der Holzkonstruktion möglich.
Für die Fernsteuerung verwende ich eine recht einfache 2- Kanalfernsteuerung, die ich für 15 € im Internet gekauf habe, bestehend aus der Bedienkonsole, einem Empfänger und 2 mitgelieferten Servos. Man braucht eigentlich nur einen Kanal, da ich noch keine Segelsteuerung eingebaut habe. Das ist etwas komplizierter. (Konstruktion von Segelwinden usw. - beim nächsten Modell!) Bei einer Standardeinstellung der Segel (etwa 30° zur Mittschiffslinie) lässt sich das Modell aber sehr gut segeln und auch wenden. Das Signal reicht einige Hundert Meter weit. So das war´s! Ich wünsch euch viel Spaß und Erfolg beim Bauen!
Falls ihr Fragen habt, könnt ihr mir gerne eine Mail schicken:
frenzel@fws-kaki.de
Jörg Frenzel
Kunstlehrer FWS Kaltenkirchen
Schablonen
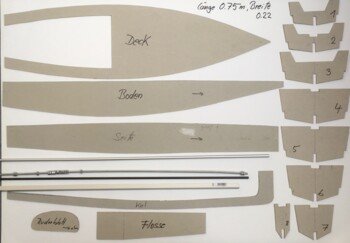
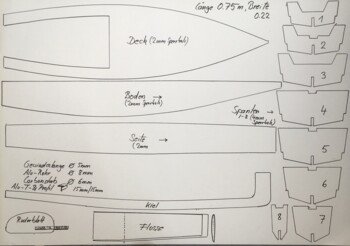
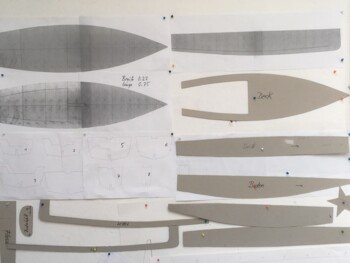