Arbeitsgemeinschaft Rollbrett
Geschrieben und durchgeführt von Moh Portuondo Alvarez
Kuck mal was da rollt! Nr. 1 eröffnet die Serie handgefertigter Unikate aus der Schülerwerkstatt. Die Bretter entsteht in Gemeinschaftsarbeit nach den Wünschen und Vorstellungen der Erbauer. Jedes Brett ist ein auf hohem Niveau gefertigtes Einzelstück.
Vom Entwurf über den Pressformbau bis hin zur Gestaltung der Unterseite werden alle Arbeitsschritte von den Jugendlichen selbst ausgeführt. Die eingelassen Plakette kennzeichnet die Herkunft und unterstreicht die Einzigartigkeit.

Und hier die Rollbrett-Serie Nr. 1.
Gebaut wurden sie von Schülern der der Klassen 7 und 8 der FWS-Uhlandshöhe. Weiter unten finden Sie eine Fotoreihe, die in der AG entstanden ist.
Longboard bau in 8 Phasen mit eine Pressform aus Beton
1. Phase Entwurf
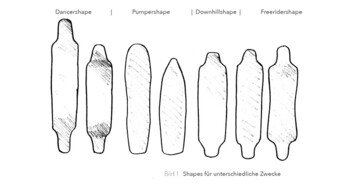
Oft lässt sich bereits an der Form des Brettes (Bild 1) der Verwendungszweck bestimmen. Nach einer Skizze, eine 3 Tafelprojektion im Maßstab 1:1 anfertigen (Bild 2).
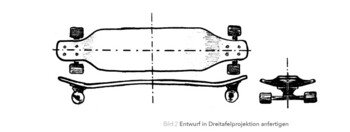
Die konvexe Form (im Längsschnitt gut zu sehen) wird in der Fachsprache auch als Camber bezeichnet. Es unterstützt den Flex, also die Fähigkeit der Durchbiegung. Dies verschafft ein weicheres Fahrgefühl und ist beim Kurvenfahren vom Vorteil da die Kraft die auf das Brett einwirkt in Bewegungsenergie umgesetzt werden kann. Die konkave Ausgestaltung der Breite (im Querschnitt zu sehen) bildet das Fußbett und gibt dem Fahrer mehr Halt.
2. Phase Pressformbau
Im Querschnitt die Materialdicke der MDF-Streifen einzeichnen aus denen dann das Pressformnegativ zusammengesetzt wird. Dann das Höhenmaße der MDF-Steifen festlegen und diese an der Formatkreissäge zuschneiden. Neben einander gestellt (Bild 3) geben die MDF-Streifen den konkaven Verlauf des Brettes wieder.
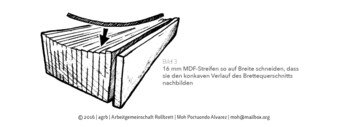
Um den Längsschnitt präzise auf die Pressform zu übertragen den Längsschnitt zunächst auf einen MDF-Streifen kopieren, aussägen und mit Hobel, Raspel und Feile ausgearbeitet (Bild 4).
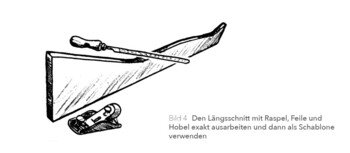
Dabei ist auf große Sorgfalt zu achten, da dieser Streifen in der Folge als Kopiervorlage für alle anderen MDF-Streifen dient.
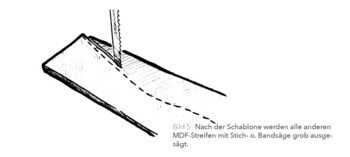
Diese dann jedoch nur grob an der Bandsäge ausschneiden (Bild 5) und dann mittels Bündigfräser und Kopierring (Bild 6) kopieren.
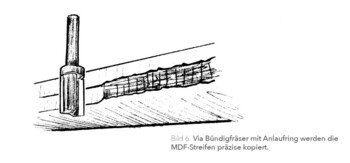
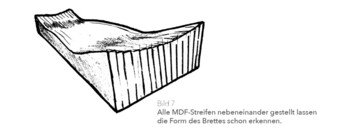
Alle MDF-Steifen in der richtigen Reihenfolge nebeneinander gestellt (Bild 7) lassen die Form des zukünftigen Brettes bereits deutlich erkennen.
Im nächsten Schritt eine Schalung bauen. Die MDF-Steifen werden mit einer 7 mm dicken Moosgummimatte abgedeckt (Bild 8).
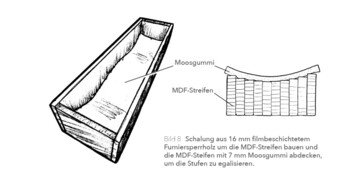
Dadurch werden die Stufen egalisiert und das Betonnegativ bekommt eine glatte Oberfläche. Die Schalung mit Betonestrich füllen (Bild 9) bis die Form an jeder Stelle mit mindestens 10 cm überdeckt ist.
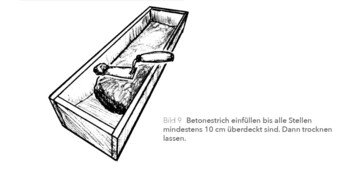
Eine Bewährung gewährleistet das der Beton den späteren Druck- und Zugkräfte, die beim Pressen auftreten, stand hält. Um die Pressformen heben zu können hab ich Platzhalter mit einbetoniert. Diese wurden nach dem Trocknen durch Griffstangen ersetzt. Nachdem die obere Betonhälfte der Pressformen getrocknet ist, die MDF-Streifen entnehmen, den Betonklotz umgedreht, neu einschalen, die Moosgummimatte aufgelegt und die zweite Hälfte der Pressform gießen. Nachdem dem Trocknen ist die Pressform fertig (Bild 10).
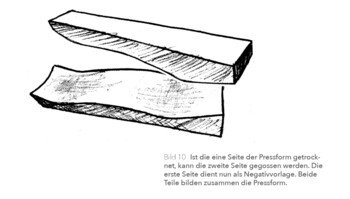
3. Phase Brettbau, Vorbereitung zum Pressen
Das Brett besteht aus kreuzweise formverleimtem Furnierholz, auch Sperrholz genannt. Durch den Wechsel der Faserrichtung in den einzelnen Schichten wird dem Bauteil Festigkeit und Formstabilität gegeben. Um zu gewährleisten, dass sich das Bauteil im Zuge von Luftfeuchtigkeitsänderung nicht in eine Richtung verformt muss der Aufbau symmetrisch sein. Das heißt die Anzahl der einzelnen Furnierschichten ist ungerade. Deck- und Mittelschicht sollten im Gleichlauf liegen. Aus ästhetischen Gründen verläuft die Deckschicht parallel zur Langseite des Brettes. Ob es 7, 9, 11, 13 oder mehr Schichten sind hängt von der Furnierdicke und der gewünschten Brettdicke ab. Ich habe mich für eine Brettdicke vom 13 mm entschieden. Das Furnier hatte eine Dicke von 1,5 mm, also ergaben sich neun Furnierholzschichten. Diese neun Schichten habe ich mit je 1,5 cm Zugabe an den beiden Seitenrändern und mit je 5 cm Zugabe an den Langenden zugeschnitten. Da alle nach dem Zuschneiden das gleiche Format hatten, musste ich sie nur noch der gewünschten Reihenfolge nach sortieren (Bild 11).
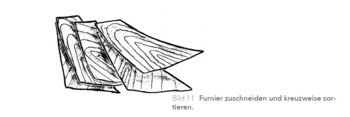
4. Phase Leimangabe und Verpressung
Die Leimangaben das Einlegen in die Presse und zum Anziehen aller Zwingen brauchte es Zeit, daher Leim mit möglichst hoher offener Zeit verwenden zB. Ponal Construct L Speed HF850. Dieser Polyurethanflächenleim (PUR) eignet sich mit einer offenen Zeit von 60 Minuten hervorragend für Formverleimungen.
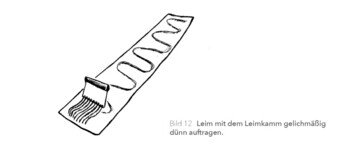
Die ausgehärteten, hellen Leimfugen sind witterungsbeständig und nahezu unsichtbar. Leim mit dem Leimkamm auftragen (Bild 12) zuvor die Fügeteile mit einem Handbesen vom Staub befreit, dann den Leim gleichmäßig dünn auftragen und die Teile aufeinander legt. Das ganze Paket in die Pressform legen (Bild 13).
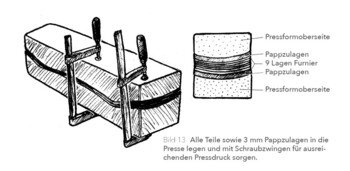
Zwingen, so fest wie möglich anziehen. Nach der Presszeit (siehe Herstellerangaben) die Zwingen wieder lösen und den Rohling aus der Pressform entnehmen (Bild 14).
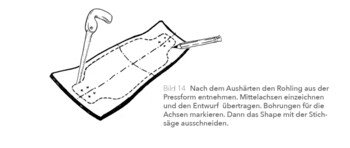
5. Phase Shapen des Decks
Eine Schablone aus Papier genau platziert machte es einfacher den Entwurf auf das Deck (der Fachbegriff für das Brett aus dem Englischen) zu zeichnen. Entlang dieser Linie das Shape (Fachbegriff für die Umrissgestaltung des Decks aus dem Englischen) mit der Stichsäge ausarbeiten (Bild 15). Die Schnittkanten anschließend mit einem Schleifklotz glätten. Es folgte das Anreißen und das Bohren der Löcher für die Achsenmontage.
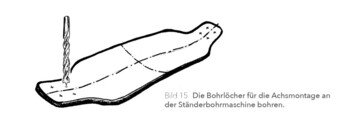
6. Phase Oberflächenbearbeitung
Kanten rundend und Oberfläche mittels Schleifklotz (Bild 16) und Schleifschwamm erst grob, dann immer feiner schleiffen.
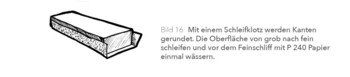
Vor dem abschließenden P 240er Schleifpapier wässern, um eine möglichst feine Oberflächengüte zu erzielen. Anschließend Deckunterseite mit einer Grafik versehen. Es folgte die Versiegelung. Ich habe mit Holzquarzöl der Firma Biofarben gearbeitet. Dieses Spezialöl lässt sich mit einem Ölballen (Bild 17) leicht aufzutragen und ergibt eine glatte, strapazierfähige und feste Oberfläche.
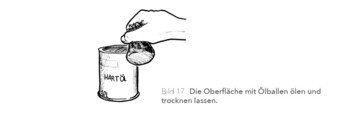
7. Phase Branding, Griptape aufbringen und Achsen montieren
Im Grunde genommen ist das Deck nun fertig. Das einzige was noch fehlte ist das Markenzeichen. Zur Auszeichnung und zur Aufwertung habe ich das Deck mit einer eingeklebten Plakette auf der Unterseite versehen (Bild 18).
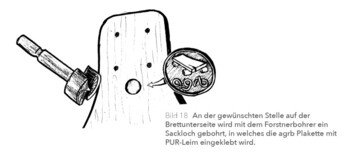
Zu diesem Zweck musste ich an der Ständerbohrmaschine mit einem 23 mm Forstnerbohrer ein 1,5 mm tiefes Sackloch bohren in welches die Plakette mit PUR Leim eingeklebt wurde. Um das Deck jedoch als Sportgerät nutzen zu können, fehlten noch zwei Dinge. Das Griptape (Bild 19) und das Fahrwerk (Bild 20).
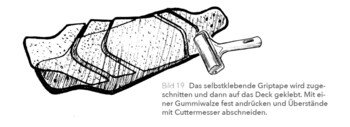
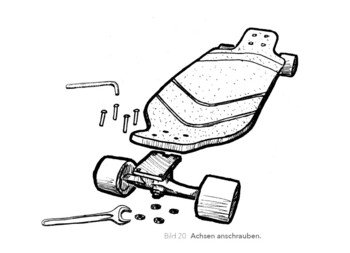
8. Phase Rollen lassen
Nun heißt es Knieschoner anlegen, Helm aufsetzen und los geht's (Bild 21).
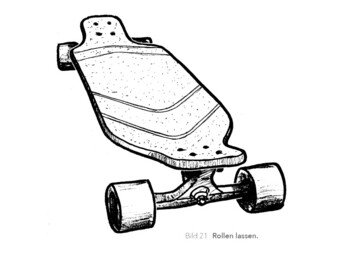
Fotoreihe
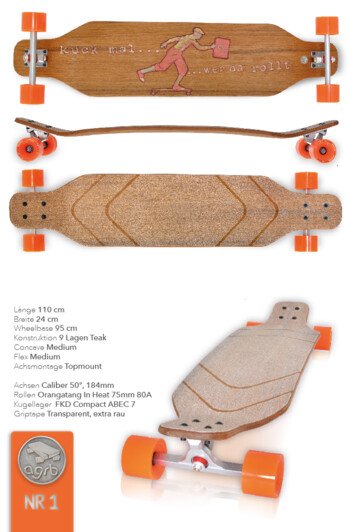
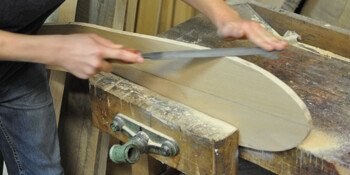

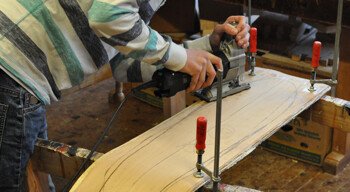
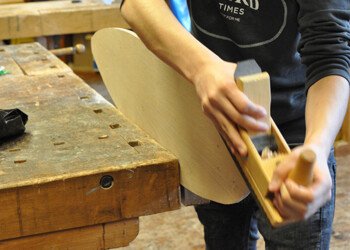
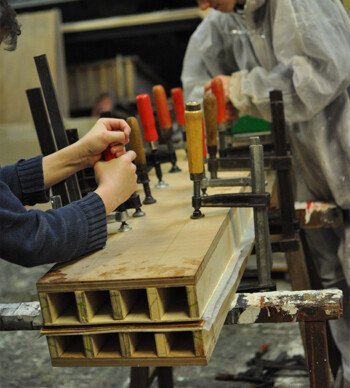
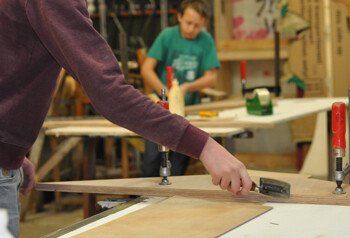
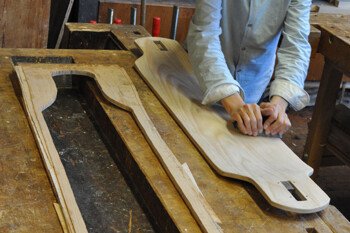
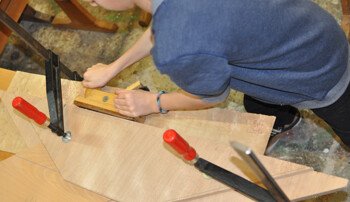
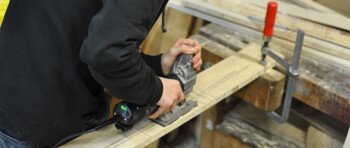
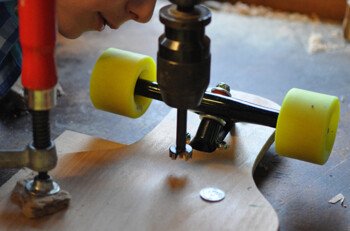
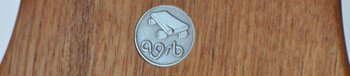
